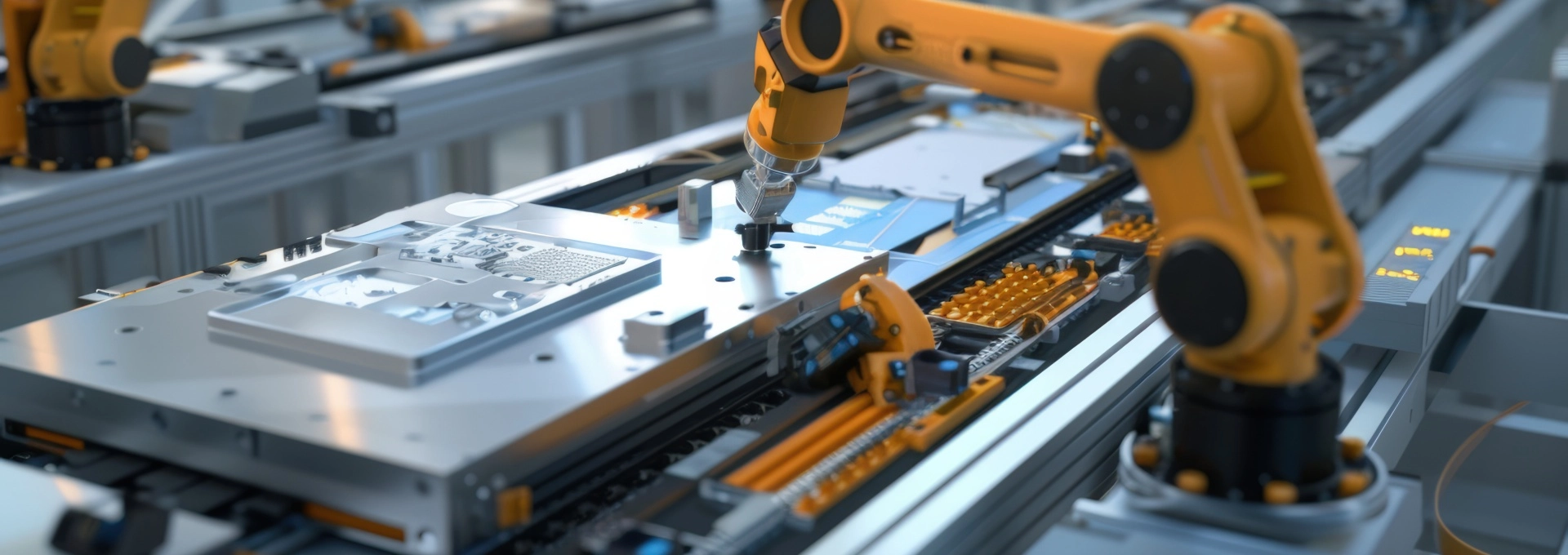
L’intégration d’établis modulables dans les lignes d’assemblage robotisées est une évolution pour l’industrie manufacturière moderne. Cette méthode novatrice combine la souplesse des postes de travail adaptables avec la précision et l’efficacité des systèmes automatisés. En optimisant l’ergonomie et en facilitant la reconfiguration rapide des espaces de production, ces options répondent aux exigences croissantes de personnalisation et d’agilité dans les processus de fabrication. L’adoption de tels systèmes permet d’améliorer la productivité, mais aussi de créer un environnement de travail plus sûr et plus confortable pour les opérateurs humains qui collaborent avec les robots.
Conception d’un établi modulable pour lignes robotisées
La conception d’un établi modulable destiné à s’intégrer dans une ligne d’assemblage robotisée nécessite une technique multidisciplinaire. Il faut prendre en compte les aspects ergonomiques traditionnels d’un établi d’atelier, mais aussi les contraintes particulières liées à l’environnement robotisé. L’objectif est de créer un poste de travail qui s’adapte aussi bien aux besoins des opérateurs humains qu’aux exigences des systèmes automatisés. La modularité est au centre de cette conception. Elle permet de reconfigurer rapidement l’espace de travail en fonction des changements de production ou des mises à jour technologiques.
Analyse des contraintes spatiales et ergonomiques
L’analyse des contraintes spatiales et ergonomiques constitue la priorité dans la conception d’un établi modulable pour lignes robotisées. Il faut optimiser l’espace disponible en garantissant le confort et la sécurité des opérateurs. Cette démarche implique une analyse des mouvements des travailleurs et des robots, ainsi que des flux de matériaux et de produits.
L’ergonomie joue un rôle important dans cette analyse. Les postes de travail doivent être ajustables en hauteur pour s’adapter à différentes morphologies et tâches. De plus, l’agencement des outils et des composants doit minimiser les mouvements inutiles et réduire la fatigue des opérateurs.
Compatibilité avec les systèmes de convoyage existants
La compatibilité avec les systèmes de convoyage existants est un aspect critique lors de l’intégration d’établis modulables dans une ligne d’assemblage robotisée. Les nouveaux postes de travail doivent s’harmoniser parfaitement avec les flux de production déjà en place, sans perturber le rythme ou créer des goulots d’étranglement.
Pour assurer cette compatibilité, les concepteurs doivent prendre en compte les dimensions, la hauteur et la vitesse des convoyeurs. Les établis modulables sont donc équipés d’interfaces standardisées qui permettent une connexion facile avec différents types de systèmes de transport. Cette méthode garantit une intégration fluide et minimise les temps d’arrêt lors de l’installation ou des reconfigurations.
Adaptation aux zones de travail des robots collaboratifs
L’adaptation aux zones de travail des robots collaboratifs est un enjeu important dans la conception d’établis modulables pour lignes robotisées. Ces postes de travail doivent être conçus pour faciliter une interaction sûre et efficace entre les opérateurs humains et les robots, en optimisant l’utilisation de l’espace.
Les établis intègrent des caractéristiques particuliers telles que des zones de sécurité clairement délimitées, des capteurs de présence et des barrières immatérielles. Ces dispositifs permettent aux robots de détecter la présence humaine et d’ajuster leur comportement en conséquence. La modularité de l’établi permet également la possibilité de reconfigurer rapidement l’espace de travail en fonction des besoins changeants de la collaboration homme-robot.
Optimisation des temps de cycle et de la cadence de production
L’optimisation des temps de cycle et de la cadence de production est un objectif central dans la conception d’établis modulables pour lignes robotisées. Ces postes de travail sont conçus pour minimiser les mouvements inutiles et réduire les temps morts, contribuant ainsi à une amélioration de la productivité globale.
Les établis modulables intègrent des fonctionnalités élaborées telles que des systèmes de stockage intelligents, des outils à portée de main et des interfaces utilisateur intuitives. Ces éléments permettent aux opérateurs de travailler plus efficacement, réduisant ainsi le temps nécessaire pour chaque tâche. De plus, la souplesse inhérente à ces postes de travail facilite les changements rapides de configuration, minimisant les temps d’arrêt lors des changements de production. L’intégration d’établis modulables dans les lignes d’assemblage robotisées peut conduire à une augmentation de la productivité allant jusqu’à 30%, en améliorant la qualité et la précision des opérations.
Technologies de modularité pour l’établi
Les technologies de modularité jouent un rôle central dans la conception d’établis adaptés aux lignes d’assemblage robotisées. Ces innovations permettent de créer des postes de travail flexibles, capables de s’adapter rapidement aux changements de production et aux évolutions technologiques. L’utilisation de ces technologies contribue au gain de productivité en entreprise, en réduisant les temps de reconfiguration et en optimisant l’utilisation de l’espace.
Parmi les technologies clés, on trouve des systèmes de fixation rapide, des plateaux interchangeables, des dispositifs d’ajustement en hauteur et des options de connectique élaborées. Ces éléments combinés permettent une souplesse sans précédent, permettant aux industriels de répondre efficacement aux demandes changeantes du marché.
Systèmes de fixation rapide
Les systèmes de fixation rapide sont une évolution majeure dans la conception d’établis modulables. Ces systèmes permettent de modifier rapidement la configuration d’un poste de travail sans nécessiter d’outils spéciaux ou de compétences techniques élaborées.
Basés sur des profilés en aluminium et des connecteurs standardisés, ces systèmes permettent une grande souplesse en garantissant une stabilité et une rigidité optimales. Les opérateurs peuvent ainsi ajouter, retirer ou repositionner des éléments de l’établi en quelques minutes, réduisant les temps d’arrêt lors des changements de production.
Plateaux interchangeables avec interface standardisée
Les plateaux interchangeables avec interface standardisée constituent une partie importante de la modularité des établis pour lignes robotisées. Ces plateaux permettent de transformer rapidement un poste de travail pour l’adapter à différentes tâches ou processus d’assemblage.
Chaque plateau est conçu pour une tâche particulière, avec des outils, des supports et des dispositifs de fixation préinstallés. L’interface standardisée assure une connexion rapide et sûre avec la structure de base de l’établi, incluant les connexions électriques, pneumatiques et de données. Cette méthode permet de réduire les temps de changement, mais aussi d’améliorer la précision et la répétabilité des opérations.
Dispositifs d’ajustement en hauteur pneumatiques
Les dispositifs d’ajustement en hauteur pneumatiques sont une innovation majeure dans l’ ergonomie et organisation du travail des établis modulables. Ces systèmes permettent d’adapter rapidement la hauteur du plan de travail aux besoins particuliers de chaque opérateur ou tâche, améliorant ainsi le confort et réduisant les risques de troubles musculo-squelettiques.
Fonctionnant à l’air comprimé, ces dispositifs permettent un ajustement fluide et précis, pouvant supporter des charges importantes. Ils peuvent être contrôlés manuellement ou intégrés dans des systèmes automatisés pour s’adapter automatiquement en fonction de l’opérateur identifié ou de la tâche en cours.
Connectique pour l’alimentation en énergie et données
La connectique pour l’alimentation en énergie et données est un aspect important des établis modulables modernes. Ces systèmes intègrent des options de connexion rapide et sécurisée pour l’électricité, l’air comprimé, et les réseaux de données, indispensables au fonctionnement des outils et des équipements de contrôle.
Les connecteurs standardisés permettent une reconfiguration rapide des postes de travail sans nécessiter l’intervention de techniciens spécialisés. De plus, ces systèmes sont conçus pour s’intégrer dans la structure de l’établi, évitant les câbles et tuyaux apparents qui pourraient gêner les opérations ou compromettre la sécurité.
Intégration des capteurs et systèmes de contrôle
L’intégration des capteurs et des systèmes de contrôle est une composante centrale des établis modulables modernes dans les lignes d’assemblage robotisées. Ces technologies élaborées permettent d’améliorer la précision et la qualité des opérations, mais aussi d’assurer une interaction sûre et efficace entre les opérateurs humains et les robots. Les capteurs et systèmes de contrôle facilitent la collecte de données en temps réel, l’optimisation des processus et la maintenance prédictive. Leur intégration intelligente dans la structure de l’établi contribue à l’amélioration de la productivité et de la flexibilité des lignes de production.
Capteurs de présence et de position des composants
Les capteurs de présence et de position des composants sont des paramètres importants pour assurer la précision et la fiabilité des opérations d’assemblage. Ces dispositifs permettent de vérifier la présence correcte des pièces et leur positionnement exact avant que les robots ou les opérateurs n’effectuent leurs tâches.
Utilisant des technologies telles que les capteurs optiques, capacitifs ou à ultrasons, ces systèmes peuvent détecter avec une grande précision la présence et l’orientation des composants. Cette information est décisive pour prévenir les erreurs d’assemblage et optimiser les mouvements des robots, contribuant ainsi à améliorer la qualité du produit final et à réduire les temps de cycle.
Systèmes de vision industrielle pour le contrôle qualité
Les systèmes de vision industrielle sont une évolution majeure dans le domaine du contrôle qualité au sein des lignes d’assemblage robotisées. Ces technologies permettent une inspection rapide et précise des produits en cours de fabrication, identifiant les défauts ou les écarts par rapport aux spécifications avec une fiabilité supérieure à celle de l’œil humain.
Intégrés aux établis modulables, ces systèmes utilisent des caméras haute résolution et des algorithmes d’analyse d’image recherchées pour effectuer des contrôles dimensionnels, vérifier l’assemblage correct des composants, ou détecter des défauts de surface. Leur capacité à traiter un grand nombre de pièces rapidement contribue à l’amélioration de la productivité en maintenant des standards de qualité élevés.
Interface homme-machine tactile pour la configuration
L’interface homme-machine (IHM) tactile facilite la configuration et le contrôle des établis modulables au sein des lignes d’assemblage robotisées. Ces interfaces donnent aux opérateurs un moyen intuitif et efficace d’interagir avec les systèmes de production, de modifier les paramètres et de surveiller les performances en temps réel.
Dotées d’écrans tactiles haute résolution, ces IHM permettent aux utilisateurs de naviguer facilement à travers différentes fonctions, d’ajuster les réglages de l’établi, de lancer des séquences d’assemblage ou de consulter des instructions de travail détaillées. Leur conception ergonomique et leur interface utilisateur intuitive réduisent le temps de formation nécessaire et minimisent les erreurs opérationnelles.
Connectivité IoT pour la maintenance prédictive
La connectivité IoT (Internet des Objets) appliquée à la maintenance prédictive est une évolution dans la gestion des établis modulables et des lignes d’assemblage robotisées. Cette technologie permet de collecter et d’analyser en temps réel une multitude de données provenant des capteurs intégrés aux équipements.
Grâce à l’analyse de ces données, il est possible de prédire les pannes potentielles avant qu’elles ne se produisent, optimisant ainsi les interventions de maintenance. Cette méthode proactive réduit les temps d’arrêt imprévus, prolonge la durée de vie des équipements et contribue à maintenir une productivité élevée. L’intégration de la connectivité IoT dans les établis modulables peut réduire jusqu’à 30% les coûts de maintenance et augmenter de 25% la disponibilité des équipements.
Sécurité et conformité aux normes industrielles
La sécurité et la conformité aux normes industrielles sont des aspects fondamentaux dans la conception et l’utilisation d’établis modulables au sein des lignes d’assemblage robotisées. Ces éléments sont déterminants pour protéger les opérateurs, mais aussi pour assurer
Respect de la norme ISO 10218 pour les robots industriels
La norme ISO 10218, particulière aux robots industriels, est une donnée à prendre en compte lors de l’intégration d’établis modulables dans une ligne d’assemblage robotisée. Cette norme indique les exigences de sécurité pour la conception, la construction et l’intégration des systèmes robotiques industriels.
Pour assurer la conformité, les établis modulables doivent être conçus en tenant compte des zones de travail des robots, des distances de sécurité et des interfaces homme-machine. Cela implique l’intégration de dispositifs de sécurité tels que des barrières immatérielles, des tapis de sécurité ou des systèmes de détection de présence, qui s’interfacent avec les contrôleurs des robots pour garantir un arrêt immédiat en cas de détection d’une présence humaine dans la zone de danger.
Mise en œuvre des dispositifs d’arrêt d’urgence
Les dispositifs d’arrêt d’urgence sont nécessaires dans un environnement industriel, et leur intégration dans les établis modulables pour lignes robotisées est importante. Ces dispositifs doivent être facilement accessibles, clairement identifiables et capables d’arrêter immédiatement tout mouvement dangereux.
Dans le contexte des établis modulables, les boutons d’arrêt d’urgence sont généralement positionnés à des endroits réfléchis autour du poste de travail. Ils sont connectés à un système de sécurité central qui, lorsqu’activé, coupe l’alimentation des robots et des équipements dangereux. De plus, des systèmes de verrouillage et d’étiquetage (LOTO – Lock Out Tag Out) sont souvent intégrés pour garantir que l’équipement reste désactivé pendant les opérations de maintenance.
Certification CE et conformité à la directive machines 2006/42/CE
La certification CE et la conformité à la directive Machines 2006/42/CE sont indispensables pour les établis modulables intégrés dans des lignes d’assemblage robotisées en Europe. Cette directive établit les exigences nécessaires de santé et de sécurité auxquelles doivent répondre les machines avant leur mise sur le marché ou leur mise en service dans l’Union européenne.
Pour obtenir la certification CE, les fabricants d’établis modulables doivent effectuer une évaluation des risques complète, documenter les mesures de sécurité mises en place, et fournir un dossier technique détaillé. Ce processus implique souvent des tests rigoureux et peut nécessiter l’intervention d’organismes notifiés pour certaines catégories de machines. Une fois certifiés, les établis peuvent arborer le marquage CE, attestant de leur conformité aux normes européennes de sécurité.
Cas de recherche : implémentation chez un équipementier automobile
L’implémentation d’établis modulables dans une ligne d’assemblage robotisée chez un équipementier automobile illustre parfaitement les avantages et les enjeux de cette technologie. Ce cas de recherche donnent des connaissances précieuses sur les aspects pratiques de l’intégration, les bénéfices réalisés et les leçons apprises au cours du processus. Pour en savoir plus sur l’ergonomie et organisation du travail, cliquez sur ce lien.
Analyse du ROI et des gains de productivité
L’analyse du retour sur investissement (ROI) et des gains de productivité suite à l’implémentation d’établis modulables chez cet équipementier automobile a révélé des résultats impressionnants. Après une période initiale d’adaptation, l’entreprise a constaté une augmentation de la productivité de 22% sur la ligne d’assemblage concernée.
Les principaux éléments contribuant à cette amélioration incluent une réduction de 35% des temps de changement de série grâce à la modularité des établis, une diminution de 18% des erreurs d’assemblage due à l’intégration de systèmes de contrôle qualité avancés et une amélioration de 15% de l’ergonomie, réduisant la fatigue des opérateurs et augmentant leur efficacité. Le ROI calculé sur une période de 3 ans a montré que l’investissement initial a été récupéré en seulement 14 mois, avec des économies continues réalisées par la suite.
Enjeux rencontrés lors de l’intégration avec certains robots
L’intégration des établis modulables avec certains robots existants sur la ligne d’assemblage a présenté plusieurs enjeux techniques et opérationnels. Le principal obstacle était la nécessité de recalibrer les robots pour s’adapter aux nouvelles configurations d’établis, un processus qui s’est avéré plus complexe que prévu initialement.
Les ingénieurs ont dû développer un protocole de communication standardisé entre les systèmes de contrôle des établis et les contrôleurs des robots. Ce processus a nécessité une collaboration étroite avec les experts pour assurer une intégration sans faille et maintenir les niveaux de sécurité requis. De plus, la programmation des robots a dû être ajustée pour prendre en compte la flexibilité importante offerte par les établis modulables, ce qui a nécessité une formation supplémentaire pour les programmeurs de l’usine.
Formation des opérateurs et adaptation des procédures
La formation des opérateurs et l’adaptation des procédures se sont révélées être des étapes critiques dans le succès de l’implémentation. Un programme de formation complet a été mis en place, couvrant l’utilisation des nouveaux établis modulables, mais aussi les aspects de sécurité liés à l’interaction avec les robots.
Les procédures opérationnelles standard (SOP) ont été entièrement revues et mises à jour pour refléter les nouvelles méthodes de travail. Cela incluait des protocoles de reconfiguration rapide des établis, des procédures de contrôle qualité intégrées et des guidelines pour l’interaction sécurisée avec les robots collaboratifs
Une approche de formation par étapes a été adoptée, avec des sessions pratiques sur des simulateurs avant le passage à la ligne de production réelle. Cette méthode a permis une transition en douceur et a contribué à réduire les temps d’arrêt pendant la phase d’implémentation.